Over the last century, the global population had quadrupled, while annual consumption of building materials has increased 42-fold[1]. Today, building and demolition are one of the largest sources of waste in the EU, where they account for around 25 to 30% of all waste[2].
With this in mind, a circular economy that promotes the maintenance and reuse of materials appears essential.
Currently, technical facilities make up around 30% of the initial cost of a new office building[3] and 27% of the environmental impact of a commercial property[4]. They are also considered a priority when developing a circular economy within the construction industry[5]. However, there is currently very little information available on circular approaches to technical facilities, and there are few practical examples.
This article presents three strategies for ensuring that technical facilities are not left behind in the transition to a circular economy: maintenance and commissioning, reuse, and reversible construction.
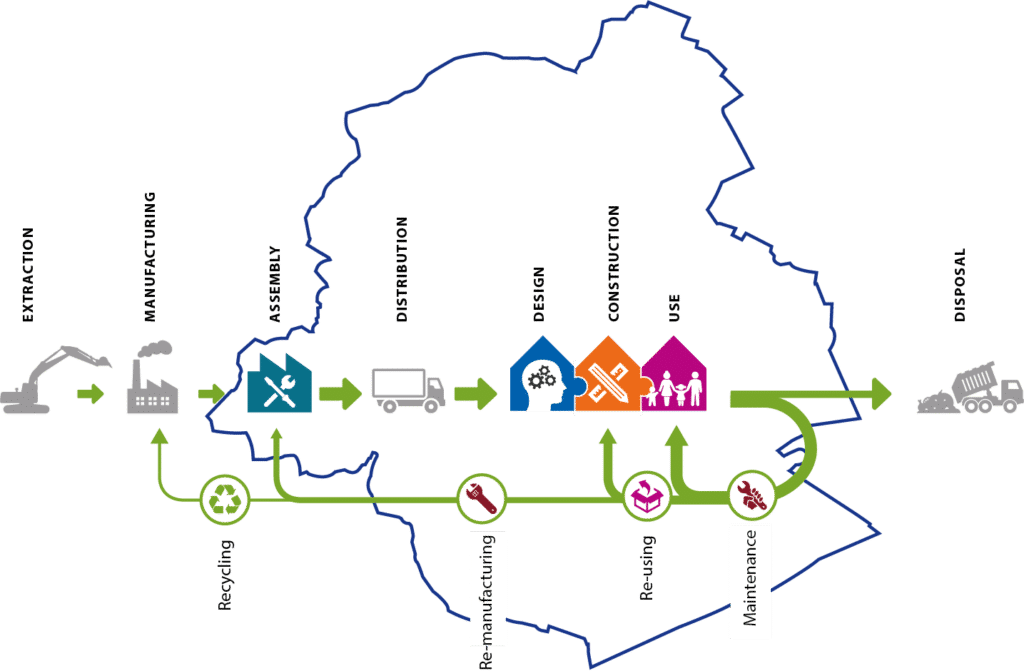
Maintenance and commissioning
Maintenance refers to “all technical, administrative and managerial actions undertaken during the lifecycle of a property in order to maintain it or restore it to a state in which it can fulfil the required function”[7].
Commissioning is the “process by which a piece of equipment, a service or a facility is tested to ensure it functions in a way that fulfils the intended purpose or specifications”[8].
While maintenance seeks to combat physical or material deterioration, commissioning enables us to combat the functional obsolescence of technical facilities.
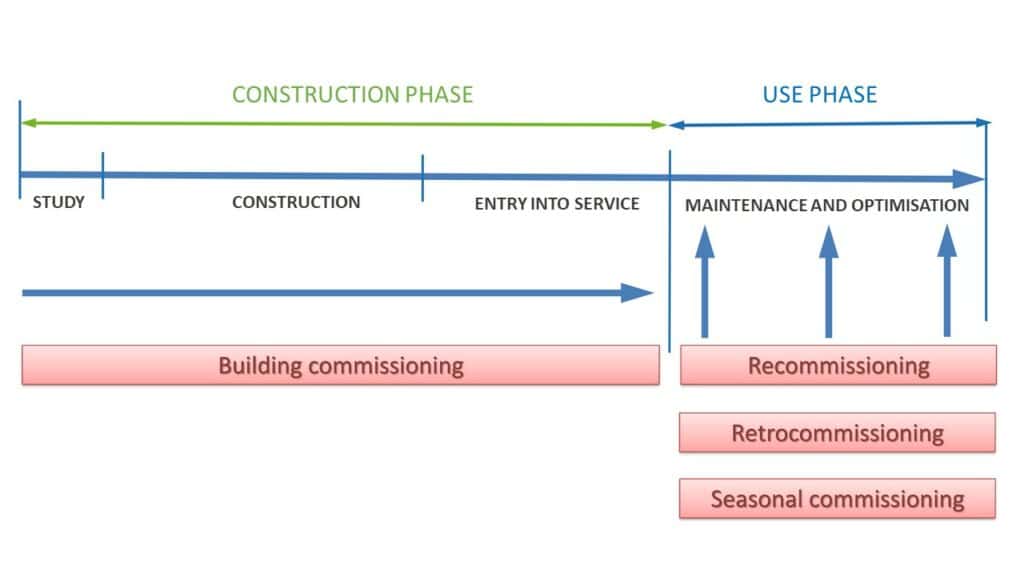
Source: Mehaudens, L., Commissioning process and sustainable building management. What exactly does it mean?, in Seminar: Commissioning: a strongly recommended step! . 2019, Brussels Environment.
From a circular perspective, these strategies are a clear priority as they extend the lifespan of technical facilities.
Reuse (or urban mining)
Reuse of building materials encompasses all practices that involve “reusing [building materials or components salvaged during demolition] for the purpose for which they were originally designed”[9]. Like maintenance, this strategy extends the lifespan of technical facilities.
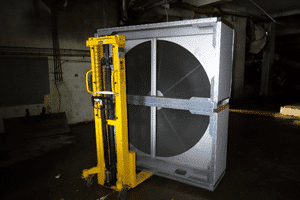
Currently, this process is not always straightforward, as it requires a high level of communication, coordination, and research. Carrying out redeployment work of this type also demands great agility from all stakeholders.
Effective maintenance, reversible design of technical facilities, and thorough documentation should help remove these obstacles in the future[10].
Reversible design
Reversible design is defined as “the design of buildings that can easily be deconstructed, or whose components can easily be added or removed without damaging the building or the products, components or materials”[11]. A distinction is made between short term reversibility, to react to a change in the usage of a space (from an office to a boardroom, for example), and long term reversibility, for more fundamental changes to the use of a space, (for example converting an office into a school)[12].
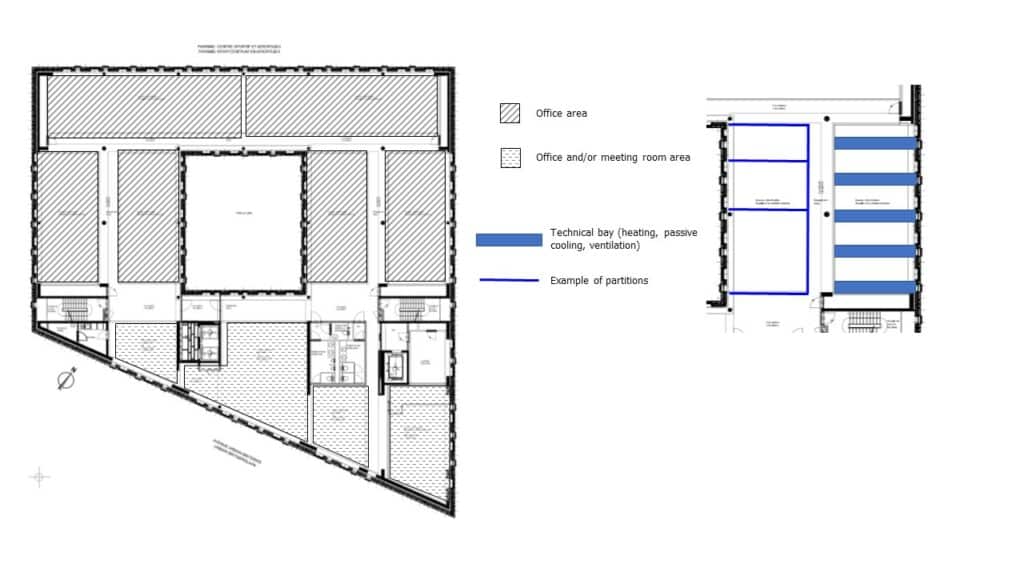
While certain practices, such as the installation of modular, movable partitions, are already commonplace, the reversible design of technical facilities is still in its infancy.
It poses an interesting challenge for design teams today, developing the buildings and facilities of tomorrow.
Authors: Anne-Laure Maerckx and Sébastien Loreau, Cenergie
Main picture: Salvaging a ventilation unit for reuse © CSTC
Read also: COVID Safe Certificate: The beginning of a solution from engineers and architects?, Training for more circular construction in Brussels, Greenbizz II, an exemplary centre dedicated to the circular economy, Clear thinking about public space, a sustainabilty catalyst
[1] Krausmann, F., et al., Growth in global materials use, GDP and population during the 20th century. Ecological economics, 2009. 68(10): p. 2696-2705.
[2] European Commission. Construction and Demolition Waste (CDW). 2019; Available from: https://ec.europa.eu/environment/waste/construction_demolition.htm.
[3] Romnée, A. and J. Vrijders, Vers une économie circulaire dans la construction. 2018.
[4] Chau, C.K., et al., Environmental impacts of building materials and building services components for commercial buildings in Hong Kong. Journal of Cleaner Production, 2007. 15(18): p. 1840-1851.
[5] Athanassiadis, A., Economie circulaire dans le secteur de la construction à Bruxelles : Etat des lieux, enjeux et modèle à venir. 2017.
[6] Brussels Environment, Feuille de route des acteurs de la construction à Bruxelles. Vers une économie circulaire. 2020, Brussels Environment.
[7] NF, NF EN 13306 : Terminologie de la maintenance. 2001, Association Française de Normalisation.
[8] Rixen, R., Comment se donner les moyens de suivre correctement ses installations techniques ? Point de vue d’un maître d’ouvrage, in Séminaire : Commissioning : une étape fortement conseillée ! . 2019, Brussels Environment.
[9] European Commission, Directive 2008/98/EC of the european parliament and of the council of 19 november 2008 on waste and repealing certain directives (waste framework directive). 2008.
[10] Maerckx, A.-L., Envisager le réemploi des installations techniques. Case study: réemploi du groupe de ventilation de la tour De Brouckère pour la rénovation du siège d’Aquafin à Aartselaar, in Séminaire : L’économie circulaire appliquée aux installations techniques. 2020, Brussels Environment.
[11] Durmisevic, E., WP3 reversible building design. Reversible building design guidelines. BAMB report. 2018.
[12] Declercq, J., Adaptabilité et réversibilité des installations techniques: importance de la conception technique et architecturale. Illustration des limites et opportunités sur base de cas concrets, in Séminaire : L’économie circulaire appliquée aux installations techniques. 2020, Brussels Environment.