Agglomerated stone is a composite material made of cement and/or resin and an aggregate and/or mineral fillers used in buildings as a finishing material for floors and walls and for the creation of sculpted objects. Use of the material grew between 1880 and 1950, a period during which over 407 patents for agglomerated stone were filed in Belgium. There is currently renewed interest in the material for several reasons, notably thanks to its beneficial environmental impact given that it promotes the circular economy and the rational use of materials (reuse of quarry waste). In a context in which the use of resources in the construction sector is surprisingly high, companies are turning to modern digital manufacturing technologies which stimulate innovation in, among other things, the design and restoration of items. Digital manufacturing is the application of digital modelling and technologies to the production of customised material items. It is, therefore, a new opportunity for restoration in the field of agglomerated stone. The creation of items in this material can be done directly by additive manufacturing or indirectly via the creation of moulds in which the material is poured. The moulds can also be created using additive or subtractive manufacturing.
Additive manufacturing in the construction sector involves the development of two types of technologies: powder and extrusion techniques. In powder-based techniques (also called Binder Jetting), a binder is selectively added to a bed of ceramic powder (5 to 10 mm thick) using a print nozzle to bind the layers together to create the solid pre-designed item, one layer at a time. Over the past years, sculptural elements with complex shapes have been created using high-resolution powder printing with a high degree of geometrical freedom and within a reasonable time-frame. This process is still being optimised (i.e., which types of materials can be used with the technology).
Additive manufacturing of agglomerated stone materials using extrusion techniques consists in extruding the “printable” material (with a different composition and rheology from the traditional material) using nozzles of different sizes to create a layered structure. Most of the studies on producing objects using extrusion follow the same steps: a first step consisting of modelling the object using 3D software, which is then cut into layers using special software. The second step consists in creating the object using a multilayer extrusion system. The fundamental difference between the different printing technologies is seen in three main aspects: the design of the print machine, the composition of the material to be printed and the technological application of the material to be printed. In restoration, the sculptural elements to be created are often very refined. This involves the use of small nozzles and the specific rheological properties of the agglomerated stone. This means that it will often be easier to create moulds using 3D modelling of the object in which the agglomerated stone objects will be poured.
The subtractive manufacturing of moulds is done in two steps: the 3D modelling of the object and the creation of its negative using different software programs and the machining of the moulds by automated milling based on the 3D model. The extraction can be done in several types of materials such as machinable wax or wood. The agglomerated stone material is then poured into the moulds. As a result, its composition is identical to that of the traditional material.
The production of objects for restoration using agglomerated stone and digital manufacturing technologies is a growing field with a great deal of potential, as well as many challenges for the coming years. Which is why the Belgian Building Research Institute (BBRI) is currently working on these topics via several research projects.
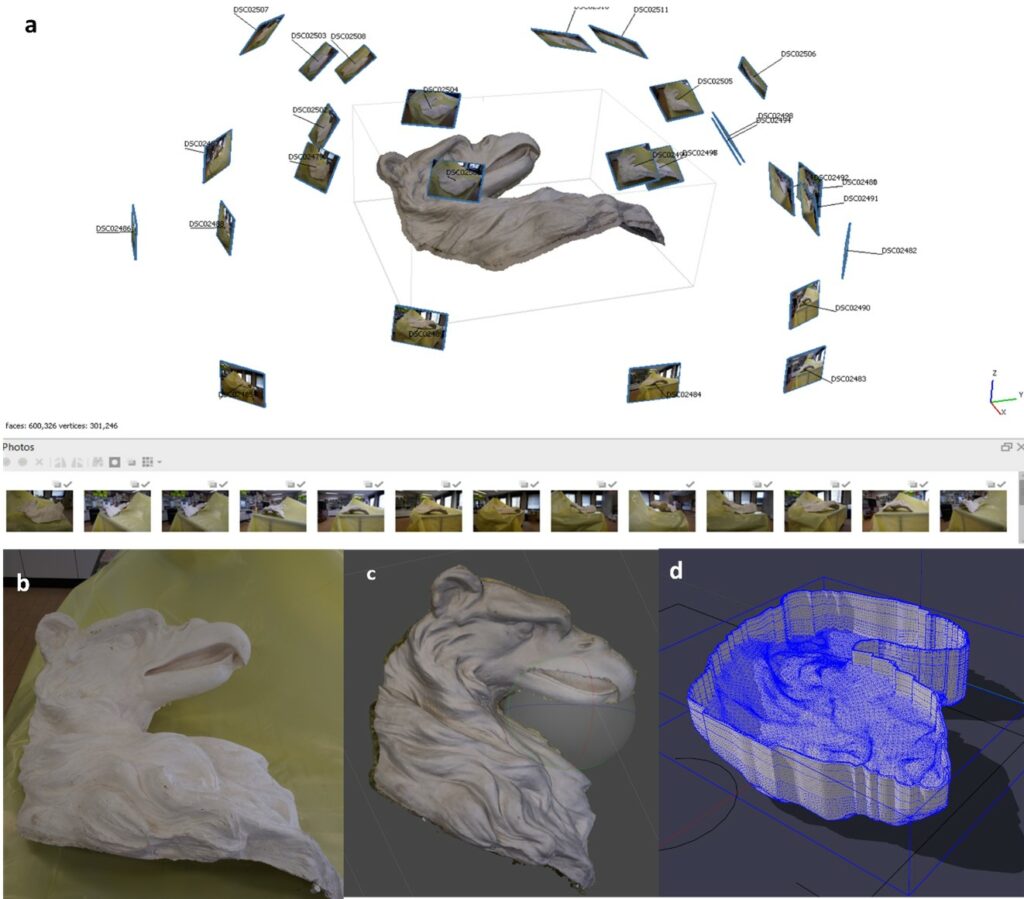
For additional information, contact the BBRI via its free “C-Tech”support service: C-Tech (cstc.be)
Authors: Julie Desarnaud and Michael De Bouw, CSTC
Read also: For responsible builders; Estimation of requirements and circularity; The social economy unites partners with respect to sustainability; Biosourced insulation: a growing market for renovation companies