Since 2006, the Brussels Regional Urban Development Regulations (RRU) have required the greening of flat roofs of more than 100 m². The benefits of generalising this practice can be measured at different scales, from the building concerned to overall well-being in the city. Among the major challenges that Brussels has set itself, the improvement of air quality, thermal regulation and the reduction of emissions are encouraging us to make our city as green as possible and use our roofs as additional green spaces.
Beyond the positive advances (increase in biodiversity and water retention), however, generalising the presence of green roofs raises a series of questions about the materials used and their origin.
The first issue is the frequent presence of lava rock (+/- 90% of the volume), which is used to lighten and drain green roofing mixes. The closest deposits to Brussels are in the Massif Central and Germany. The exploitation and transport of these materials have a significant impact on their carbon footprint.
Another debatable issue is the use of peat-containing substrates. This fossilised organic material comes from open-pit mining or from underground strata. These are unique environments that are home to rare, very specific and often protected fauna and flora. Subterranean peat, on the other hand, is relatively stable, buried carbon storage; once exposed to the elements, these materials decompose and release their carbon into the atmosphere, increasing the amount of atmospheric CO2, with the consequences we are all aware of. This peat has a main structural objective, which is to lighten the substrates and guarantee better water retention.
In addition, these substrates contain a large number of fertilisers and acidity correctors. Over time, these substances are consumed or washed away by rainfall. This leaves a material that is low in nutrients and too acidic in pH. This seems a long way from the original intention of green cities.
Lastly, for practical reasons, many contractors use pre-cultivated plates. Despite their relatively high cost, they guarantee a quick, low-tech job and an immediate result. However, they lead to the use of significant quantities of plastic (between 5 to 7 kg per m²).
In addition to these “details”, there are problems with the partitioning of the plants. The majority of the pre-cultivated slabs are composed of a structure comparable to a succession of flowerpots placed next to each other. This considerably limits their root development and therefore also their foliar development. The other disadvantage is related to the lack of inertia in terms of humidity. For the roof, this will result in a lack of development of entire areas and therefore a direct impact on the aesthetics of the hanging garden.
Fortunately, there are environmentally friendly and even eco-circular alternatives.
A mixture of crushed bricks (from brick or tile demolition sites) and sieved compost (from the decomposition of green waste) is an ideal substrate for these mostly succulent plants. The icing on the cake is that the thin concrete cement and mortar remains act on the pH by making the environment alkaline, which is perfectly suited to these plants.
These resources are available in phenomenal quantities in Brussels and could be reused on an ultra-local scale. For years, we have achieved various successes in this direction and can observe excellent vegetal development in the long term. Note that some manufacturers are now offering substrates made from recycled materials.
We hope that in the future, greater account will be taken of the origin and composition of substrates in the drafting of specifications.
This could generalise the use of substrates with a much more beneficial ecological impact.
We just have to change our mentalities and our good old habits.
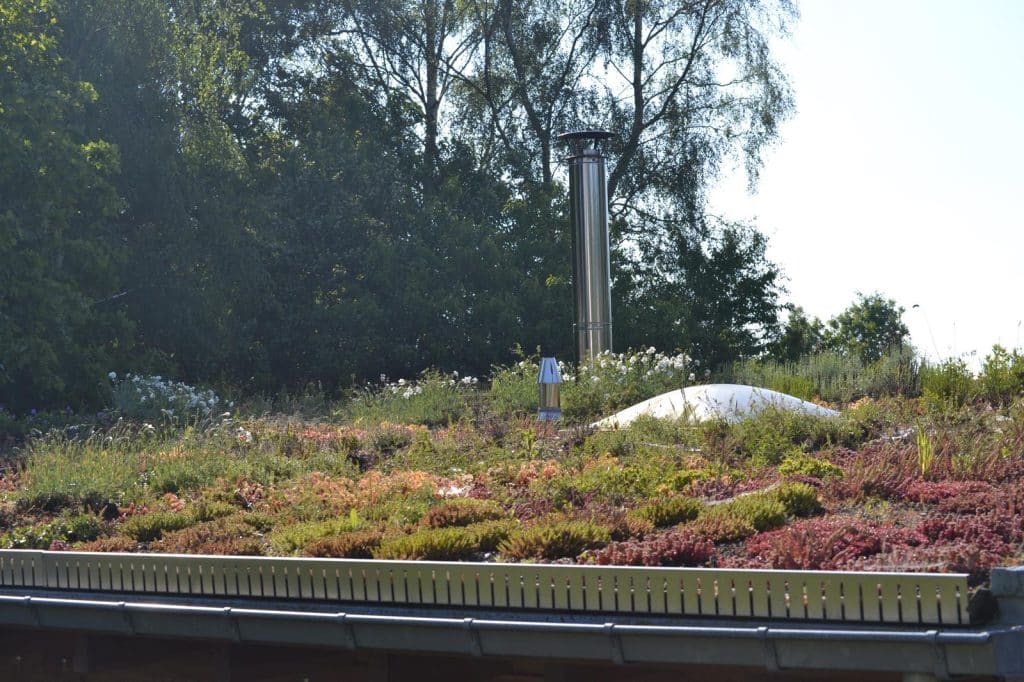
Author : Eric Frère, La Ferme nos pilifs
Read also : From now on, architecture must (absolutely) be inspired by nature; Using electrical engineering for energy transition; ORI highlights the role of consultancy and engineering firms in Brussels; Agglomerated stone and digital manufacturing techniques to restore heritage buildings