At a time when the construction sector is being forced to rethink its practices in response to the climate emergency, wood is emerging as a material of choice. In Belgium, however, it is still only used to a limited, even marginal extent in certain market segments, although there are increasing signs that this trend is changing. ecobuild.brussels spoke to industry experts Hugues Frère (Hout Info Bois) and David Roulin (ArtBuild Architects), and in this article they present a nuanced assessment of the current situation, combining structural findings, technical perspectives and environmental convictions.
Expertise, but no organised network
With around 120 companies working in timber construction nationwide, the Belgian landscape remains relatively modest, with just one truly specialised company in Brussels. The rest of the economic fabric is made up mainly of very small structures, often working in the joinery or carpentry sectors.
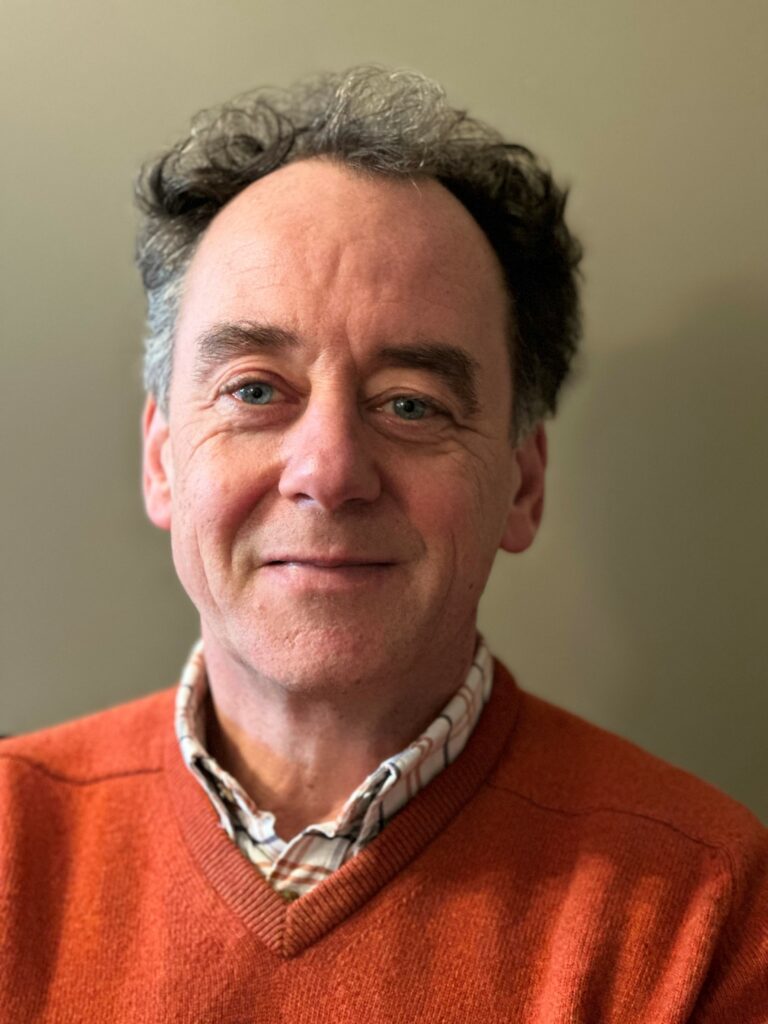
“The majority of companies in the industry are working on fewer than ten timber construction projects a year, which illustrates how much the sector is still dominated by very small businesses,” explains Hugues Frère. This fragmentation hinders the professionalisation of the sector and the emergence of structured industries.
Photo: Hugues Frère, director of Hout Info Bois
In the Flemish region, prefabrication and “turnkey” practices allow for better industrial organisation, while in Wallonia, despite a long history of expertise, growth remains cautious. “It’s a paradox: we have the skills, but we’re not using them enough in a collective dynamic,” emphasises David Roulin.
Photo: David Roulin, CEO of ArtBuild Architects (copyright Bénédicte Maindiaux)
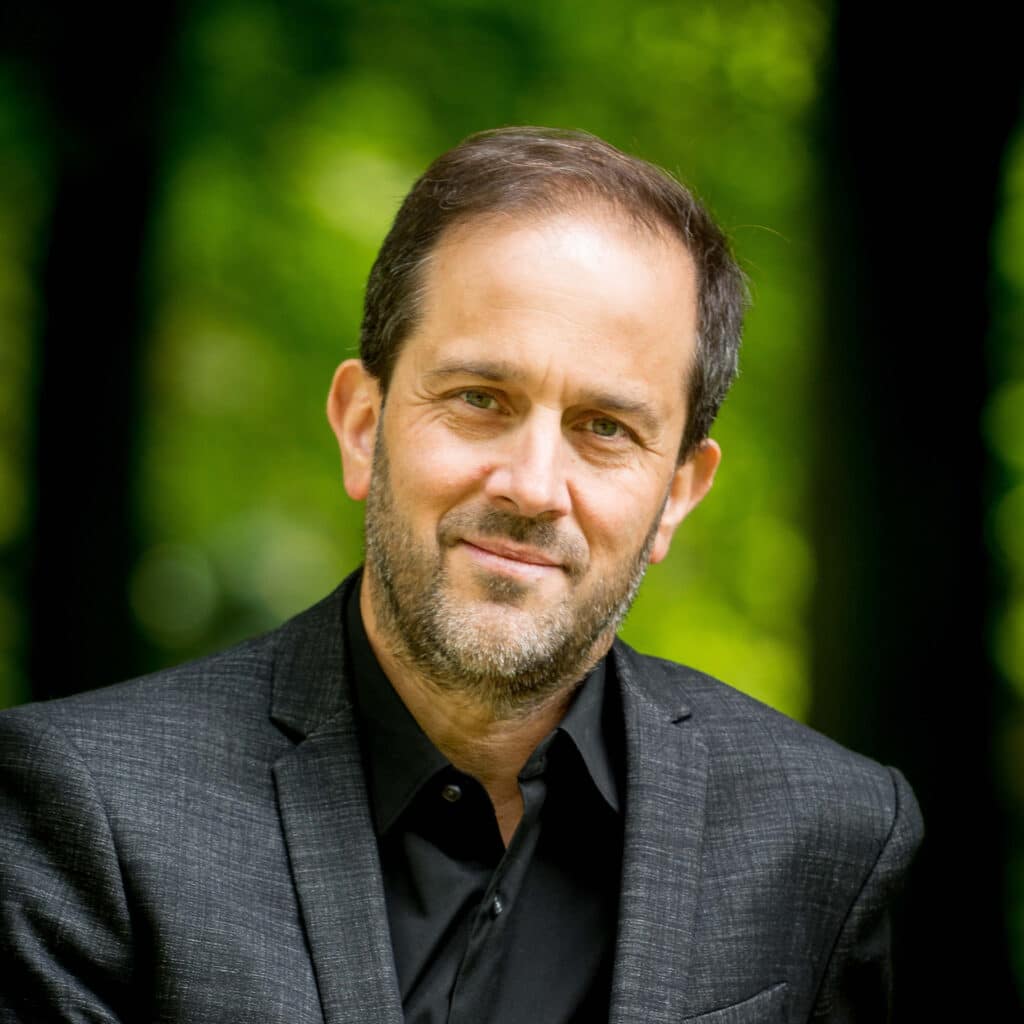
Brussels: pioneering in energy, but lagging behind in materials
At Belgian level, the Brussels-Capital Region is seen as a pioneer in adapting building regulations, particularly in terms of energy efficiency. However, these adaptations are not yet taking the issue of building materials into account enough at present. “In 2015, the Region imposed the passive standard, and everyone followed suit. Why not do the same for wood?” asks David Roulin.
Yet, there are clear advantages to using wood in dense urban environments. It’s a very light material, which means it can be built on top of existing structures, often without reinforcing them. “In Brussels, all you have to do is look at a satellite map: all the flat roofs have enormous building potential,” says Hugues Frère. Wood is perfectly suited to the task, as it is quick to install and causes little disturbance on the construction site.
A few recent projects demonstrate this potential, but they remain the exception rather than the norm. Wooden architecture has not yet established itself as an automatic response in public calls for projects or private real estate contracts.
Belgian trailing behind Europe, but boasting high quality
Compared to the achievements of its neighbours, Belgium is struggling to keep pace. France has imposed quotas for the use of bio-sourced materials in public procurement contracts. In Austria and Scandinavia, timber construction is a cultural and industrial standard. “If we take our close neighbours as a benchmark, France is ten years ahead of us. And even Luxembourg is starting to overtake us,” David Roulin observes.
But Belgium can hold its head high on a technical level. “Our regulatory requirements in terms of energy performance have pushed companies to develop real expertise,” Hugues Frère emphasises. In his opinion, this explains why the quality of construction in Belgium is often superior to that of more advanced countries accustomed to building with wood.
The challenge is therefore not so much one of competence, but, with the help of political support, scaling up public procurement to encourage the use of wood, and the development of a stronger market structure.
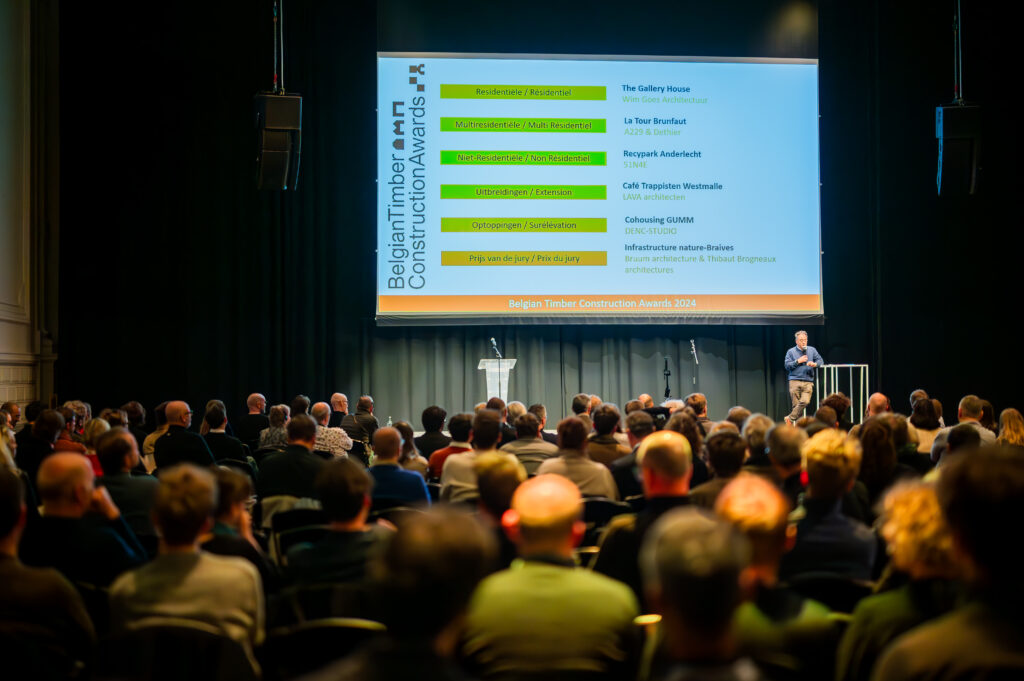
Is cost actually an issue?
The question of cost is regularly cited as a barrier to the use of wood. However, according to our two experts, this perception needs to be nuanced. “In France, when the obligation to use bio-sourced materials was introduced, wood was more expensive than traditional materials such as steel and concrete. Ten years on, the gaps have narrowed greatly, and in some cases even reversed, thanks to economies of scale and increased competition,” David Roulin points out.
In Belgium, the limited number of players capable of responding to large-scale timber construction tenders prevents this trend from occurring: “In the absence of competition, these players dictate the law of the market, and the principle of supply and demand doesn’t come into full effect. This context of timber construction in Belgium explains, at least in part, the higher cost of wood compared to other traditional building methods,” he explains.
However, there are many other arguments in favour of timber construction when it comes to cost. As soon as plans are made for a wood project from the design stage, its economic efficiency becomes clearer. Indirect savings (site duration, modularity, fewer finishing touches, coordination) are also a factor.
Crucial assets to build on
In addition to its low carbon footprint, wood also stands out, as timber construction can be completed very quickly. “A timber house was recently built on my street. To carry out the work, they had planned to block the street for a week. After just two and a half days, the structural work was completed, and the street was re-opened to traffic,” Hugues Frère recalls.
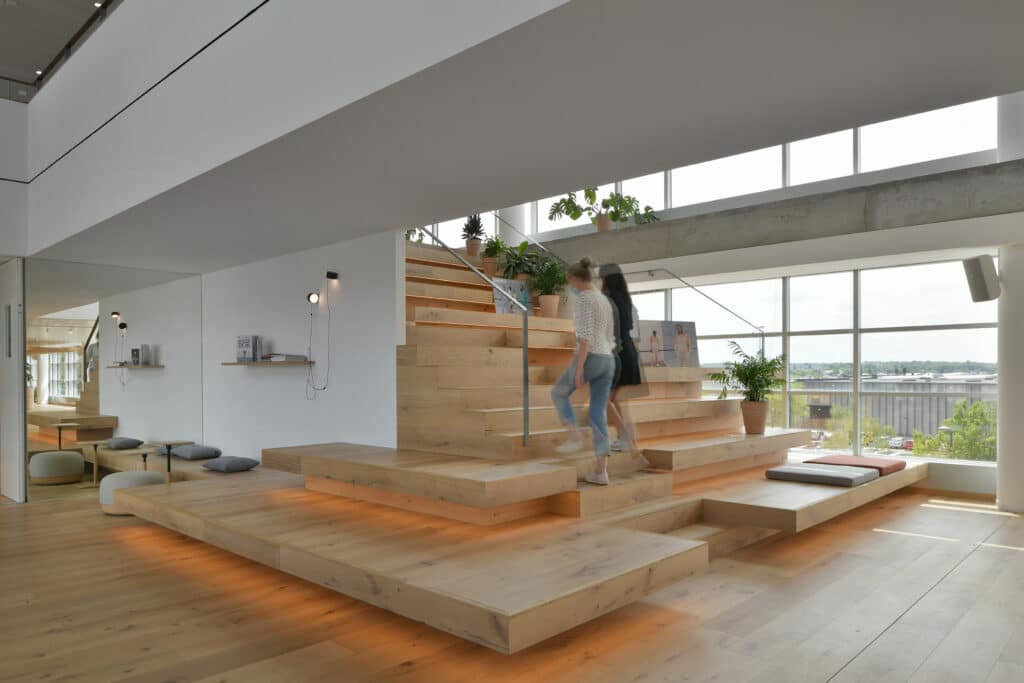
David Roulin also emphasises the impact on individuals: “It’s been scientifically proven that wood has a positive effect on well-being. It’s the notion of biophilia: the smell, touch and sight of natural materials have a positive effect on our body.”
Photo: Headquarters of Stanley Stella, eco-responsible textile company, Brussels (copyright Serge Brison)
Wood represents an opportunity for professionals, too. It encourages more modern practices, attracts new skills and drives the integration of digital technologies and prefabrication techniques. These advantages are also a response to the shortage of skilled labour in the sector, thanks to cleaner, more industrialised and more rewarding working methods, which are, above all, less arduous work for workers.
Rethinking the framework: from materials to circularity
The real breakthrough lies not just in the choice of wood, but in a new approach to construction. The idea is to rethink buildings as modular, adaptable systems that can be dismantled. “We’ve been working for over ten years on designing in preparation for reuse and off-site construction. But for this to be systematically rolled out on a large scale, a fundamental cultural transformation is needed,” David Roulin explains.
Wood, with its structure, lightness and ease of assembly, lends itself particularly well to this mindset. It becomes a natural ally to those taking a circular approach working in the re-use economy. “It’s a transitional material in every sense of the word: technical, ecological, and beneficial to the health of everyone involved,” he adds.
Clear levers to make use of
To create this virtuous momentum, the two experts are calling for a clear political signal. “Public procurement must assume its role as a driving force. We’ll win over the rest of the market by setting an example,” David Roulin insists. He’s also calling for incentives to be put in place, such as bonuses for low-carbon projects, support for the industry, tax breaks, etc.
Hugues Frère highlights the TOTEM tool developed to measure the environmental impact of buildings: “Small companies need to be able to integrate their products into this tool. Today, an EPD costs €15,000, which is out of reach for these businesses.”
Both lament the absence of a major trade show in Belgium dedicated to bio-sourced construction, like the one organised every year in France. “We’re campaigning for a Brussels edition of the International Wood Construction Forum dedicated to the Benelux countries. This is where a common culture is forged, where ideas are shared,” David Roulin concludes.
The need for concrete action and why we should believe in it
The conditions are all in place: technical expertise, willing stakeholders, inspiring examples. The only thing left to be done is to make the most of this opportunity, by strengthening support mechanisms, boosting supply and triggering demand. Wood construction can no longer remain the exception; it must become a norm in a sector aiming to be sustainable, intelligent and responsible.