La pierre agglomérée (PA) est un matériau composite à base de ciment et/ou résine et de granulats et/ou charges minérales utilisé dans les bâtiments comme matériau de finition des sols, de façades et pour la création d’éléments sculptés. Ce matériau s’est développé entre 1880 et 1950, période dans laquelle on recense plus de 407 brevets « pierre agglomérée » en Belgique. Il y a un actuellement regain d’intérêt pour ce produit pour plusieurs raisons, notamment l’impact environnemental bénéfique de ce matériau car il favorise l’économie circulaire et l’utilisation rationnelle des matériaux (réutilisation des déchets des carrières). Dans ce contexte où l’utilisation des ressources dans le secteur de la construction est étonnamment élevée, les entreprises se tournent vers les technologies modernes de fabrication digitale qui stimulent l’innovation dans, entre autres la conception et la restauration d’objets. La fabrication digitale est l’application de la modélisation numérique et des technologies à la production d’objets matériels personnalisés. Elle représente donc un nouvel horizon dans le domaine des matériaux PA pour la restauration. La création d’objets dans ce matériau pourra ainsi se faire directement par fabrication additive ou indirectement par la création de moules dans lequel sera coulé le matériau. Ces moules peuvent aussi être réalisés par fabrication additive ou par fabrication soustractive.
La fabrication additive dans le secteur de la construction implique le développement de deux types de technologies : les techniques à base de poudre et les techniques d’extrusion. Dans les techniques basées sur les poudres (également appelées Binder Jetting), un liant est déposé de manière sélective sur un lit de poudre céramique (d’une épaisseur d’environ 5 à 10 mm) à l’aide d’une buse d’impression, liant ces zones ensemble pour former la pièce solide préconçue, une couche à la fois. Ces dernières années des éléments sculpturaux de forme complexe ont été produits par impression de poudre, avec une haute résolution et un degré élevé de liberté géométrique dans un délai raisonnable. Ce procédé est encore en cours d’optimisation (i.e. type de matériaux utilisables avec cette technologie).
La fabrication additive de matériaux PA par extrusion se produit lorsque le matériau « imprimable » (ayant une composition et une rhéologie différente du matériau traditionnel) est extrudé par des buses de différentes tailles pour former une structure en couches. La plupart des études de production d’objet par extrusion suivent les mêmes étapes : une première étape qui consiste à modéliser l’objet, grâce à un logiciel 3D qui sera ensuite découpé en couches grâce à des logiciels spécifiques. La deuxième étape concerne la réalisation de l’objet grâce à un système d’extrusion du matériau en couches. La différence fondamentale entre les différents technologies d’impression provient de 3 principaux aspects : le design de l’appareil d’impression, la composition du matériau à imprimer et l’application technologique du matériaux à imprimer. Dans la restauration, les éléments sculpturaux à réaliser sont souvent d’une grande finesse ce qui entraine des tailles de buses petites et des propriétés rhéologiques spécifiques du matériaux PA. Ainsi il sera souvent plus aisé de réaliser des moules à partir d’une modélisation 3D de l’objet dans lesquels seront coulés les objets en pierre agglomérée.
La fabrication soustractive des moules se fait aussi en deux étapes : la modélisation 3D de l’objet et la création de son négatif grâce à différents logiciels et l’usinage des moules par fraisage de manière automatisé à partir du modèle 3D. L’extraction peut se faire dans plusieurs types de matériaux comme la cire usinable ou le bois. Le matériau PA est alors coulé dans les moules. Sa composition est ainsi identique à celle du matériau traditionnel.
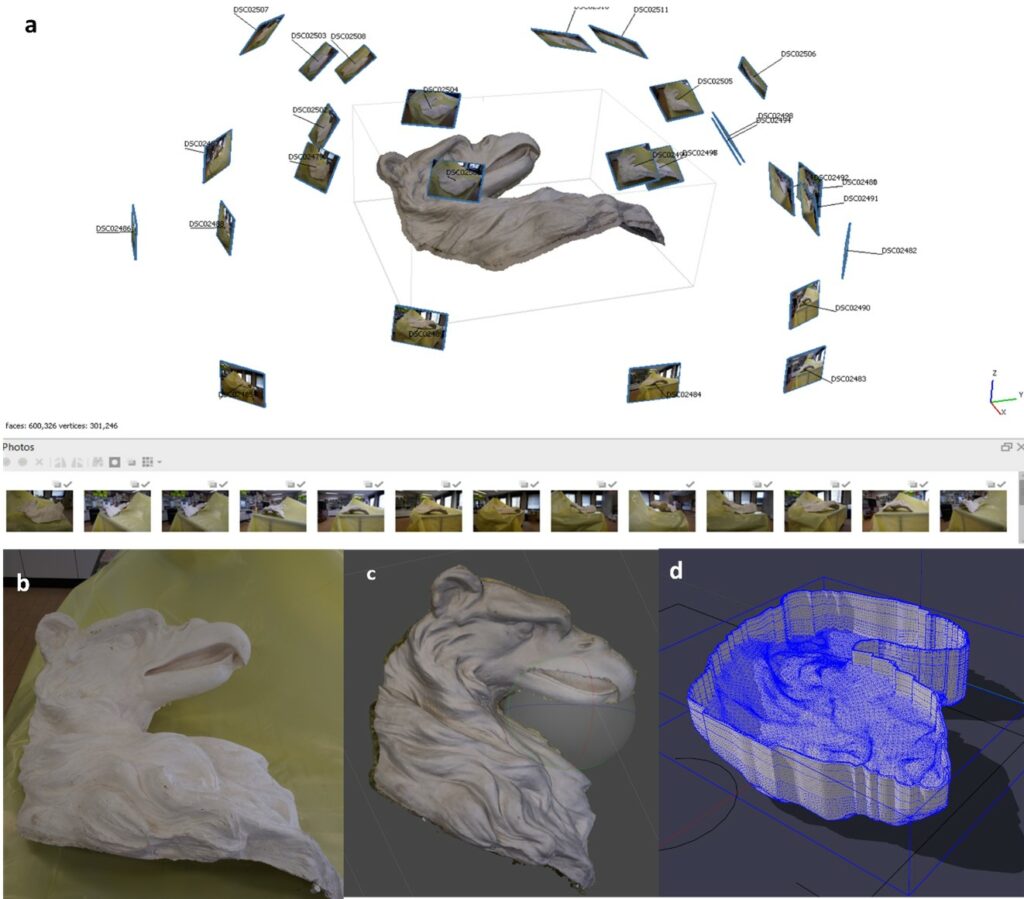
La production d’objet pour la restauration à base de pierre agglomérée grâce aux technologies de fabrication digitale est un domaine en plein essor avec beaucoup de potentiel, mais aussi de nombreux défis pour les années à venir. C’est pourquoi le Centre Scientifique et Technique de la Construction (CSTC) travaille actuellement sur ces sujets au travers de plusieurs recherches
Figure 1 : (a) Processus de création du modèle 3D par photogrammétrie du bas-relief du griffon ; (b) modèle en plâtre (c) modèle 3D généré à partir de la photogrammétrie et son négatif (d) qui servira de base pour la production de moules.
Pour toute information complémentaire, les entreprises intéressées peuvent faire appel au CSTC via son service de support gratuit « C-Tech » : C-Tech (cstc.be)
Auteurs: Julie Desarnaud et Michael De Bouw, CSTC
Lisez aussi: Pour des bâtisseurs responsables; Programmation des besoins et circularité; L’économie sociale réunit des partenaires autour de la durabilité; Les isolants biosourcés : un marché d’avenir pour les entreprises de rénovation